
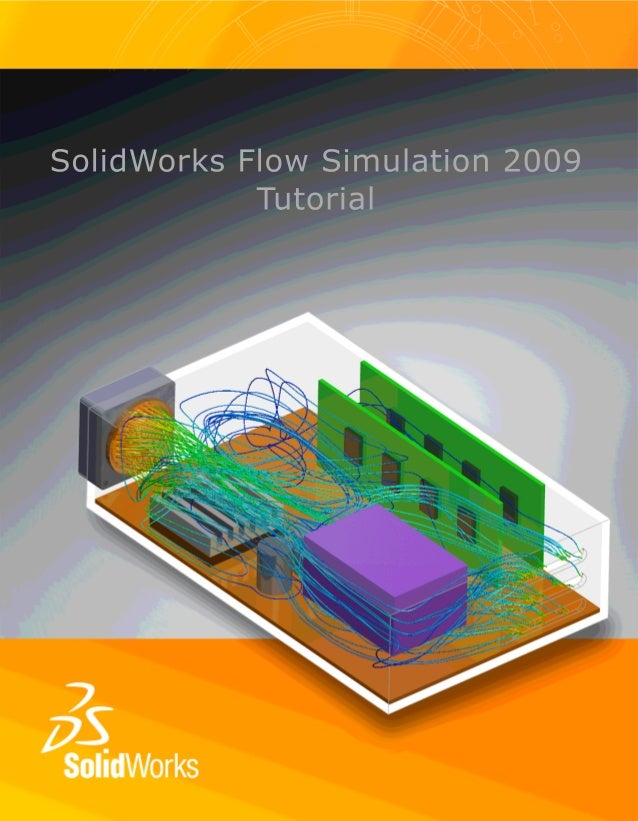

And I think we've got a thermoelectric cooler in there, and of course, the chips themselves have been selected for their cooling. And we're cooling those things via heat pipes. In order to kind of simplify things, we've got a single exhaust fan on this case, just trying to get the heat out. In this case of a compact PC, a compact personal computer where we got really just one mainboard with some components on it. And so, let's think of a case study where we might be using some of these tools.
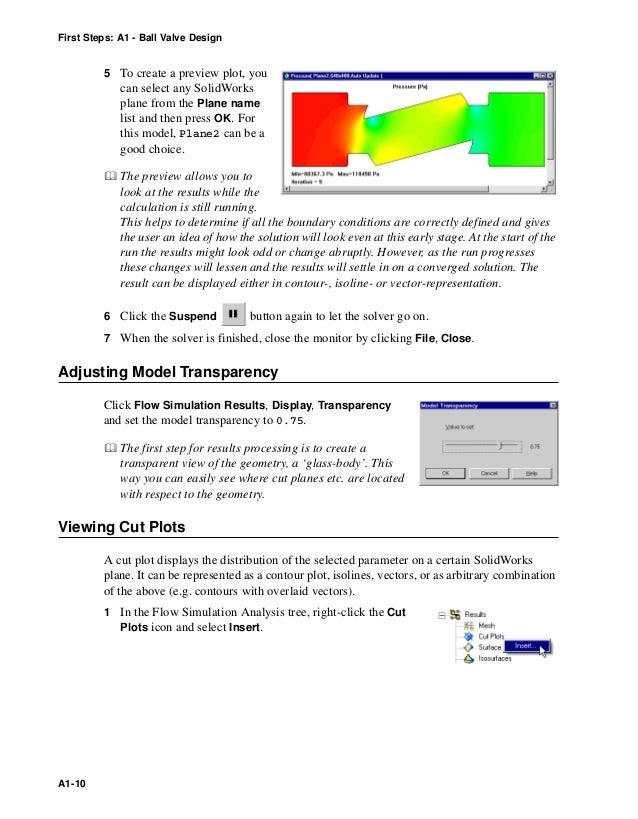
And of course, those are highly integrated with the design tools, which generally are going to be SOLIDWORKS. So of course, uh, in the solution portfolio at orca systems right now we're talking about the simulation family of products. We're going to look at how you could use solid works to have an integrated or what we call design validation process where you can take some of that information from the suppliers of these components and put it into SOLIDWORKS to increase the accuracy of your results. In addition to whatever kind of heat-sink we might be trying to create, or how we decide to create the vents or component placement on the circuit board. So if we want to make sure that we are checking these thermal requirements, and we're getting the best mechanical design, we want to make sure that we are capturing those electrical design features as accurately as possible so that we know if, for example, the chip itself has been designed in a certain way to get the heat out or we're accounting for that too. And while we might be trying to look at some mechanical design of changes, such as moving fans around, putting vent in an enclosure, or designing a heat-sink - in a lot of cases, whether or not the chip can stay at a proper temperature is also dependent on how that internals were designed or other aspects of let's say the layers and PCB or cooling devices that we might use that are more sophisticated. But in a lot of cases, a big part of that cooling is going to be something that was already designed into the board itself or maybe even inside the components. But in many cases, if you're like me, you found yourself in a situation where a product that you might be designing or validating needs to be cooled. Throughout the years, I've managed to learn a little bit about circuit boards and components that may go on them. That's what my design work background was. I'm sure like many of you out there, the typical SOLIDWORKS user among our customer base is mostly going to have a mechanical design background.
#MODELING NATURAL CONVECTION IN SOLIDWORKS FLOW SIMULATION SOFTWARE#
We will be focusing on something that we don't talk about a lot, which is when you're getting to the point where you're planning on doing the setup for one of these things, what capabilities there are in the software that let you actually take whatever the real world data is about the product that you might be will find, and how you actually can put that into the software and make sure that the results you're getting out are accurate. I'll be going through one of the most popular applications for this product which is performing analysis on some sort of electronics product to check temperature constraints. I'm the product manager for Flow Simulation. Welcome to the webinar Wednesday presentation of From Datasheets to Results, which is thermal analysis with the SOLIDWORKS Flow Simulation Electronics Cooling Module.
